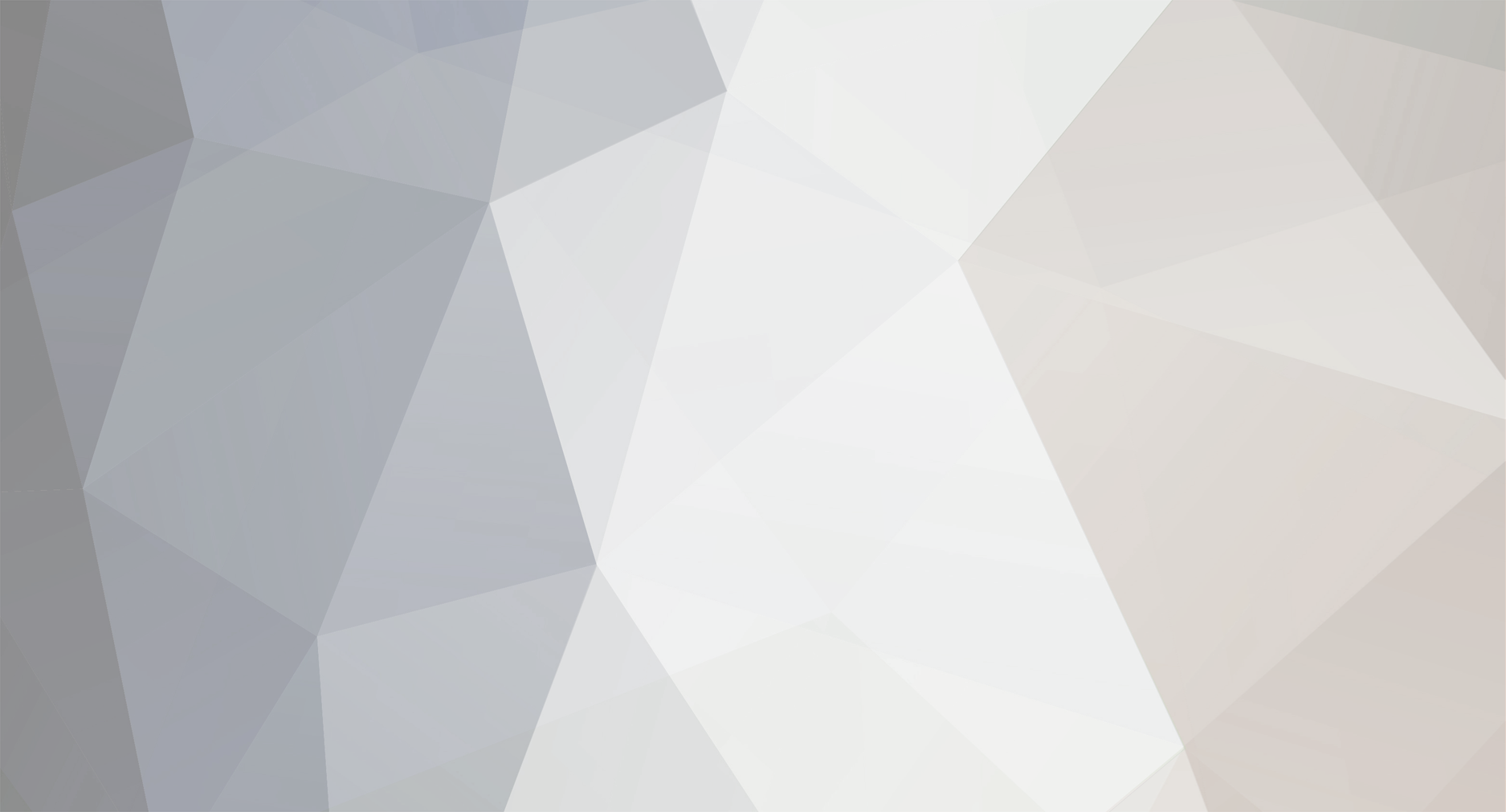
B.Sin
-
Content Count
1,676 -
Joined
-
Last visited
Content Type
Profiles
Forums
Calendar
Posts posted by B.Sin
-
-
18 hours ago, DIO said:
So this has become a wish list 😂😂😂 ?
Yes!
-
MiG-25.
F-22.
F-35A,B,C.
Su-15.
Su-24.
The list could go on!
😉
-
14 minutes ago, Mr Matt Foley said:
Word! Kitty Hawk is supposed to bring one to us, but I would gladly spend extra for anything GWH brings us.
WORD!
-
1 hour ago, falcon91352 said:
May be a hint to the next G.W.H. project after the Su-27?
That would be sweet!
-
Nigel, I appreciate your efforts!
And thank you for the unboxing
of the B-52 video! Looking forward to seeing your more detailed review of the subject!
Brad
-
4 hours ago, Rocketdrvr said:
Now where is that "JEALOUS" Button???
Ha!
-
On 7/20/2020 at 5:53 AM, Curt B said:
How far have you gotten on a model before giving up?
I am am so frustrated with myself, I want to cry. I’ve been working for weeks on a 1/48 Eduard Fw190 D-9, and yesterday, while trying to complete the paint, I completely messed up! I was trying to do a ‘by hand’ interface between the 2 main colors, and suffice to say that I REALLY messed up the paint work. If this was Tamiya paint, I might be inclined to get the paint off the model using Windex...I’ve done that before. However, in the case, one color is Mission Model, the other is Mr. Color Aqueous. I didn’t get so angry with myself as to throw the model in the trash or break it, but this model has just been frustrating from the beginning. I’m just curious about all of you...how far in a model build have you gotten before calling it quits? What do you do, or have you done with those models? Stomp on them, break them, throw them in the trash, or just set them aside in a ‘shelf or closet of shame’, maybe to one day be looked at again, weeks, months, years hence, in case at one time you’ll think of a way to address the horrible mess you made of the tank or airplane? Just curious what you do or have done with your disasters...
I feel your pain!
-
-
Come on Kittyhawk, tool a Yak-41 Freestyle in 1/48th scale!!!
-
1 hour ago, ya-gabor said:
Hi Brad,
This is a very good question! I have been pushing this for some time, but as you know I am only a small part in this team and the manufacturer makes all the decisions of what, where and when to show.
Actually some images of the real plastic have been shown already, even if in a non authorized way.
I for one also hope that soon real images will be shared by G.W.H
Best reagards
Gabor
Thank's Gabor.
-
Gabor,
When will we see some plastic?
Brad
-
1 hour ago, psimon said:
If you don't like Kitty Hawk's "sh!tty" products, why are you here on this topic? Thanks to members posting images we can all see for ourselves some of the issues we may need to deal with if we choose to buy these kits. We are looking for positive solutions to some of the issues not some one whining about why they hate the company.
THINK, WHAT TO DO!
-
On 7/11/2020 at 2:06 AM, Mfezi said:
Fantastic attention to detail. I know this kit won't be cheap, but at the slow rate at which I complete models, it looks like it will be very well worth it!
I don't mind paying for quality!
-
21 hours ago, ChesshireCat said:
I doubt it. Maybe in the $100K range on a good day. Head light buckets are held to less than an arc second all over to focus the light beam. A model kit could be off .008" and nobody's gonna know it. But when you run it across a CMM or Shadowgraph; that error looks as big as your thumb. I was in and out of that plant at least once a week, and often two and three days at a time. I was after the latest technology in powdered metal casting, and how to build a mold.
Without getting too technical, and also thinking about the curves in an airframe. It takes two measuring devices to duplicate this. As the machine runs each device talks to the other thru the computer. This is done with a very special program in a "canned cycle". Each program like this is very closely guarded. It's written either by inside folks or the actual machine tool manufacturer with a letter of confidentuallity following it. I used several owned by different groups of people that had no sense of humor. You steal the software, and all they do is read it line by line, and the Feds come knocking on your door. I know of one bunch in Japan that got the greeting, and are still paying. To be exact, you can't even down load the programs to a disc. They won't load! They come off a main frame to the CNC control, and are locked. Takes an act of congress to make an edit in one. Very few machines have a dual read axis drives (I can only think of six or seven, and three are out of business).
gary
Thank's!
-
It would me nice if GWH included
F.O.D. in the kit.
-
5 minutes ago, JeffreyK said:
errr, no. More like 80-150K.
J
Errr, thank's.
-
14 minutes ago, ChesshireCat said:
honestly, I have no serious idea. Yet I know that with the basic depth of the cut with a sinker you are thinking less that 1.5". That's critical. Then figure the rough cut at .005" a minute. Or about 2.5 hours including setup time. Programing will get you for something like two hours total if your good at your craft. After roughing it out, you go back into the metal with a semi finish cut at about .002" a minute. Your only taking about .005" all the way around unless it something super critical. Then you will go back in a third time and sorta fuzz off about a thousandth of an inch with the finished master. Pretty much an all day affair. That's for one spru set. The real issues you run into are with irregular cures. Running the EDM isn't all that bad, but making the master is a bear. Have no idea what Raymond pays for an hour of machine time on an EDM, but fifteen years ago I was spending well over five hundred an hour on a big ELOX and had it's own power transformer outside the building. It didn't matter what you did, the minute you turned that beast on it was five hundred bucks. Cutting with it would seriously increase the light bill to close to a grand an hour if you turned the power way up. I only used that beast when I just had to. Otherwise I used smaller machines, and even then it was usually a wire EDM.
I might toss in here that what I called programing was to run the machine, not design the part. I have no idea how many hours it took to do that part. Making the masters take a good bit of work. You chip the master, and you start all over. I've seen masters with almost a weeks labor in them. Copper inert tungsten is so expensive the the government regulates the sales of it. I don't remember why we used it sometimes, but the raw stock was kept locked up. Never saw big pieces, and think we mostly used it for threads and internal splines in a blind hole. I might add here that if you get a power surge, or anykind of loss in power; you start all over!
Twenty years ago, each mold for the head light buckets on a car cost two to three million a piece. You had to have a minimum of three each, and in some cases six to eight of each.
gary
Wow! So, is it save to say it could cost two or three million dollars to produce a kit?
-
8 hours ago, ChesshireCat said:
very true! I never knew all that much about injection molding till I spent about a month learning from folks who knew the subject. They were making molds to within a half arc second with blended compound curves In 410SS steel. One mold was worth two to three million dollars, and they were mirror imaged to each other.
gary
Wow! So, tell me, with an educated guess, what do you think the cost of tooling was for the F-104?
-
1 hour ago, ChesshireCat said:
99% of us have little if any idea what EDM machine time cost per hour. Let alone the electricity bill. Trust me it's pretty heavy. 410 and 420 stainless steel in the sizes needed ain't cheap as well, and Raymond may have seen the light and gone to an even better steel and multi times the price. Then you get to cut the masters used to cut the molds. Some use graphite while folks with deep pockets use copper inert tungsten ($$$$). Either way the master is in the trash can at the end of the cycle.
Folks have been asking for this airframe and that airframe. I can think of two:
1/48th F100 series
1/32 A37 Dragonfly
gary
You can't make an omelet, without breaking a few eggs!
LOL
-
I don't know if I will live long enough to see it!
-
26 minutes ago, Raymond Chung said:
Dear delide,
The retooling of the small place is same as new tooled F-104A/C, so unless it has a strong reason, we rather put the investment to other new item than retool it.
Yes, I believe same as every maker, they do have something omitted, for us, nose, canopy, intake shape, wing shape is unfixable from the consumer, so we put high priority in those area.
Everything from the "back" would classified as "less" critical. In our validation process, we have a named "15-mins" rules. Where after all the shape is validated by us and contributors, we will pass to a newbis who has no idea about it. Give him 15 mins and if he cannot identify any shape error, the 3D CAD can move on.
To our experience, the experts team who devote into the project usually make the biggest mistake on basic shape or even dimension issue. So, in our workflow, we will ask someone who does not run the project and ask him to have a snap check. 90% of the time, the newbie usually discover some basic flaw and sometimes lead to overall redo the entire CAD we did before.
Kinetic is 10 years old already and we flight for different stage of improvement from shape validation, technical issue such as fitting, parts breakdown..... now we are moving into the stage to try to deliver the details with reduced parts count and also user friendless in assemble and painting. We don't drill into breaking parts to eliminate aftermarket replacement. Instead we try to classify the "need" of the group of customers where we try to serve the widest range of average modellers need and leave the room to aftermarkets+basic kit for advance modeller.
We take building a model like a travel experience, do the same kit with different experience with different options - OOB, superdetails, mass array building.
We define the "Gold Series" label to let customer identify those kits under the new engineering standard. Not only the tooling quality, we actually work back from the injection system to the tooling specification. To make sure the the parts cannot only be "tooled" out, but also consider the long running injection quality stable condition - we move from QC to Process Control. Thus, the tool made now will consider whether the dedicated injection system can be produced in a stable way. We have put excessive investment in the injection system where it is no way to find a subcontractor with such equipment to do subcontracting for us.
Those effect has appear on the F-104G product and now you will see the Harrier GR1/3 and IA-58 and see how far we go since the F-16.
Dear Mr. Chung,
Would you consider producing a new F-16 series to you gold standard tooling?
Brad
-
-
On 7/5/2020 at 3:36 PM, Raymond Chung said:
Dear Thomas,
We address this issue in TF-104 and coming F-104A/C when we receive and recheck the issue. For you the shape error is a factor that you would not take this kit as your choice, I respect that. But at the same time, other kits form from other brand has also some sort of issue. In 1/48, Hasegawa one is 1/49.5 not 1/48. So, each kit has it pro and cons and you as a consumer have to choose base on your needs.
As for the TF-104, we take your feedback and luckily we are on time to revise the part before going to tooling, so the TF-104, F-104/AC will have this small issue resolved. As for F-104G, we evaluate that we will not do anything on it as cost to recover it to "your" comment is not worth the fiscal effort. Sorry that we are not running model contest to win the prize, we are running a business to provide consumer product with cost, budget concern. Just like TAMIYA F-4 in 1/32 posses some shape issue on the E/J model, unless you have a better option, as a modeller either you live it that or fix it yourself or find another alternative.
If you want to stay a fair suggestion to the other people, you should also mention the compete pictures of all alternative pros and cons, instead of just putting focus on the one of the difficult to notice (of course not for you), So, the message stated here will provide a more clear and fair comparsion.
I see you are very upset on this issue and posting all notes on facebook, forum to stand out the error to anyone who may not notice before you state it out. I am sure some one will provide you a perfect 104 sometimes at your promotion.
Nothing is perfect! Personally, I don't see anything, never did!
-
27 minutes ago, Darren Roberts said:
I'm bored. I thought I'd bring back the entertainment. 😄
BAHAHA!!!
Great Wall Hobby G.W.H L4827 1/48 Su-27UB “Flanker C” Heavy Fighter
in Jet Modeling
Posted
Let's see some plastic!