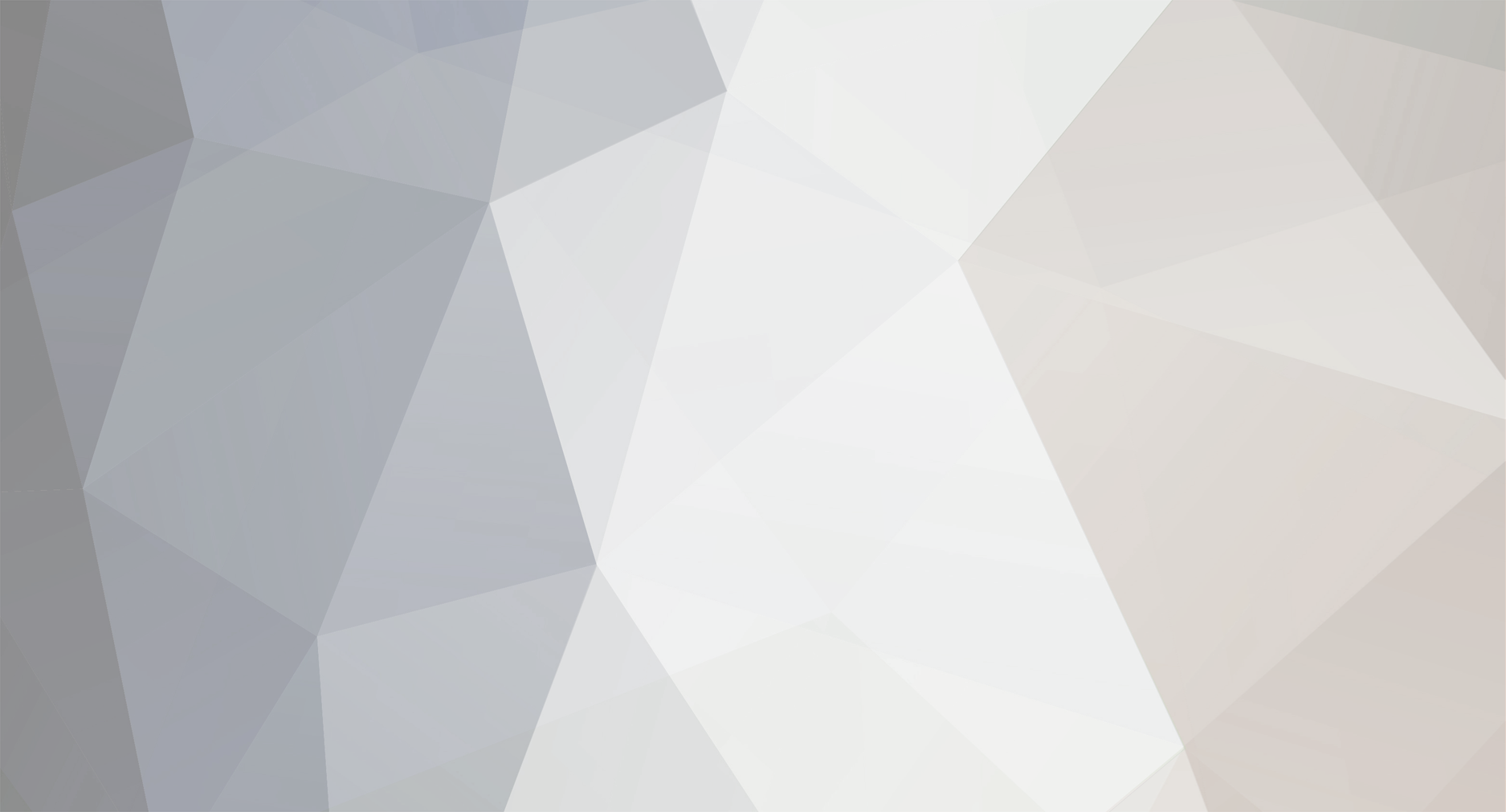
Homer
Members-
Content Count
85 -
Joined
-
Last visited
-
space shuttle stack accurate flight deck question
Homer replied to Homer's topic in Real Space Modeling
Thanks Rostko for bringing to my attention that Shapeways is now in bankruptcy proceedings. I'll look into offering the models on an alternative platform, but I'll need a little time to do so. If other modelers are also looking to purchase these parts please post here to let me know which parts you would like to acquire so I can prioritize my efforts accordingly. Thank you to the community for your support. -
space shuttle stack accurate flight deck question
Homer replied to Homer's topic in Real Space Modeling
That looks fantastic, Rostko, great job with the lighting! I'm impressed as well with your discipline in creating and placing decals on all of the tiles. How did you print opaque gray lettering decals for the black tiles? -
space shuttle stack accurate flight deck question
Homer replied to Homer's topic in Real Space Modeling
What amazing work, Rostko. Did you create your own photo-etch frames for the displays? If you get a chance, would you please post and describe the steps you used to superdetail the astronaut figures? -
space shuttle stack accurate flight deck question
Homer replied to Homer's topic in Real Space Modeling
Rosktko, that’s fantastic work, bravo! Thank you so much for posting. The third photo doesn’t appear to load correctly - would you mind reposting that one? Actually, I am so intrigued by your masterpiece, if you have more images of your intermediate steps, I would really enjoy seeing how you did your work. Please feel free to post more in this thread so that we can appreciate how you took the parts to a completely higher level of accuracy, and also how you intend to make the cap removable. -
Those parts look great! How thin are the HUD frames and the seat frames? Shapeways limits the minimum width of unsupported wires (i.e. the frames) to 0.8 mm and supported wires to 0.6 mm. https://www.shapeways.com/materials/fine-detail-plastic-3 Re: geometry matching, here’s how I did it: I got lucky, very lucky. http://orbit.medphys.ucl.ac.uk I downloaded Orbiter and looked at the game’s assets, which were fortunately stored as separate files and not compressed into one big data file. The flight deck model was actually still a Blender file, i
-
Homer started following 1/72 Revell Seats
-
Hey Rittic, great work on your seats! I had tried to make the seats in my flight deck look more accurate, with the metal frame and the rods supporting the headrest, but they were way too thin for Shapeways to print in fine detail plastic. So my seats, unlike yours, are blocky and obviously not accurate. But, as I found out once I sealed up my build, if you are building the flight deck in launch configuration with astronauts occupying all of the seats, you can't see any seat detail from any of the external windows, including the overhead ones. I
-
Homer started following 1/72 Scale Space Shuttle Challenger STS-41B on MLP and STS-71 Rollover Build 1/72 Scale
-
space shuttle stack accurate flight deck question
Homer replied to Homer's topic in Real Space Modeling
Thank you so much Rittic for introducing yourself and purchasing the upgrade parts. I look forward to following the progress with your build and learning from your approach; please feel free to post to this thread. Thanks as well for the fantastic link to the German build; that’s a really clever approach using the mesh to simulate surface textures, both for the thermal blankets and the tile. -
space shuttle stack accurate flight deck question
Homer replied to Homer's topic in Real Space Modeling
Hello SpacecraftGuy, Thank you for the kind words about the parts; I’m grateful to the community that has been so encouraging and supported the project. With regards to selling the files directly to modelers, I am not quite ready to proceed in this direction, but I will keep it in mind and consider it if this makes the most sense in the future. I hope to purchase my own resin printer in about 2-3 years and will see if the consumer level technology at that point will be sufficient to reproduce the details with these parts so that one can forego Shapeways; the Form 2 tes -
Whoops, posted to wrong thread just now. I concur with mb1k; it’s a real pleasure watching others work with these parts in their builds.
-
space shuttle stack accurate flight deck question
Homer replied to Homer's topic in Real Space Modeling
Dave (and other modelers), here is an SVG file for the paint masks for the windows and the fore RCS thruster that you can import into Cricut Design Space; good luck negotiating with your wife for Cricut usage time. I already sent you these masks in the envelope with the HUD frames, but since you have access to a digital cutter, you might find having these useful in case you need to make more paint masks. Let us know how your attempt to fit the parts into the Revell goes. window and RCS masks 2.svg -
Hello all, great work MedicModeler10! Forgive me for posting this resource that I am sure most of you have already seen, but Steven Jochums did a tremendous amount of work in coming up with his thermal blanket modeling guide that he kindly shared with the shuttle modeling community here: http://www.lakecountyspaceport.com/files/100625718.pdf I don’t know if a laser cutter could create the quilted look on a sheet of material (i.e. the orthogonal matrix of protruding bumps with the linear border outline). HotDog might be able to give us some guidance i
-
space shuttle stack accurate flight deck question
Homer replied to Homer's topic in Real Space Modeling
Thank you Pete and Medicmodeler10 for the compliments about my parts; I’m gratified that they are being received so positively by the community. Thank you to all who have purchased the parts or contributed to this thread. Pete, thanks as well for the heads up about the large volume of sanding/filling work that awaits. My build is on pause as I try to figure out how to create the tile overlay for the rest of the model surface; HotDog’s plan has a lot of promise, and I think with a laser cutter and a thin rubber membrane, it might be possible to simulate the tile pattern over the r -
space shuttle stack accurate flight deck question
Homer replied to Homer's topic in Real Space Modeling
SImon, I really like how you put the microLEDs in those aft slots that I tried to shape like the fluorescent under cabinet lights. I'm looking forward to seeing how the light from those alcoves floods the aft area when it is sealed up. JPaunicka, I completely share your the desire to forego the Shapeways middleman and print my own parts with a resin printer. I sent off the tiled roof of my beanie cap model a few years ago for a complimentary test print by Formlabs on a Form2 to see if it could produce the parts at the quality I wanted, and the tile detail wasn't quite at the leve -
space shuttle stack accurate flight deck question
Homer replied to Homer's topic in Real Space Modeling
Thanks Tracy for the vote of confidence. Will try to make the T-0 panels in 1/100 for the Tamiya model. JPaunicka, the parts are for sale now in my shop: https://www.shapeways.com/shops/homer-s-spare-model-parts -
space shuttle stack accurate flight deck question
Homer replied to Homer's topic in Real Space Modeling
Thank you both for the kind compliments. Thanks to the trial and error learning curve of the beanie cap parts, I think these aft parts came together with less mistakes. JPaunicka, I will be happy to put these parts up for sale on my Shapeways storefront. I need to get the depth of the backstop ridge adjusted (it’s part of the T-0 umbilical base piece), and then I will post the parts for sale, probably this weekend. I apologize in advance to modelers interested in buying the parts. They will not be cheap, and that’s not because of my profit margin; it’s really set by