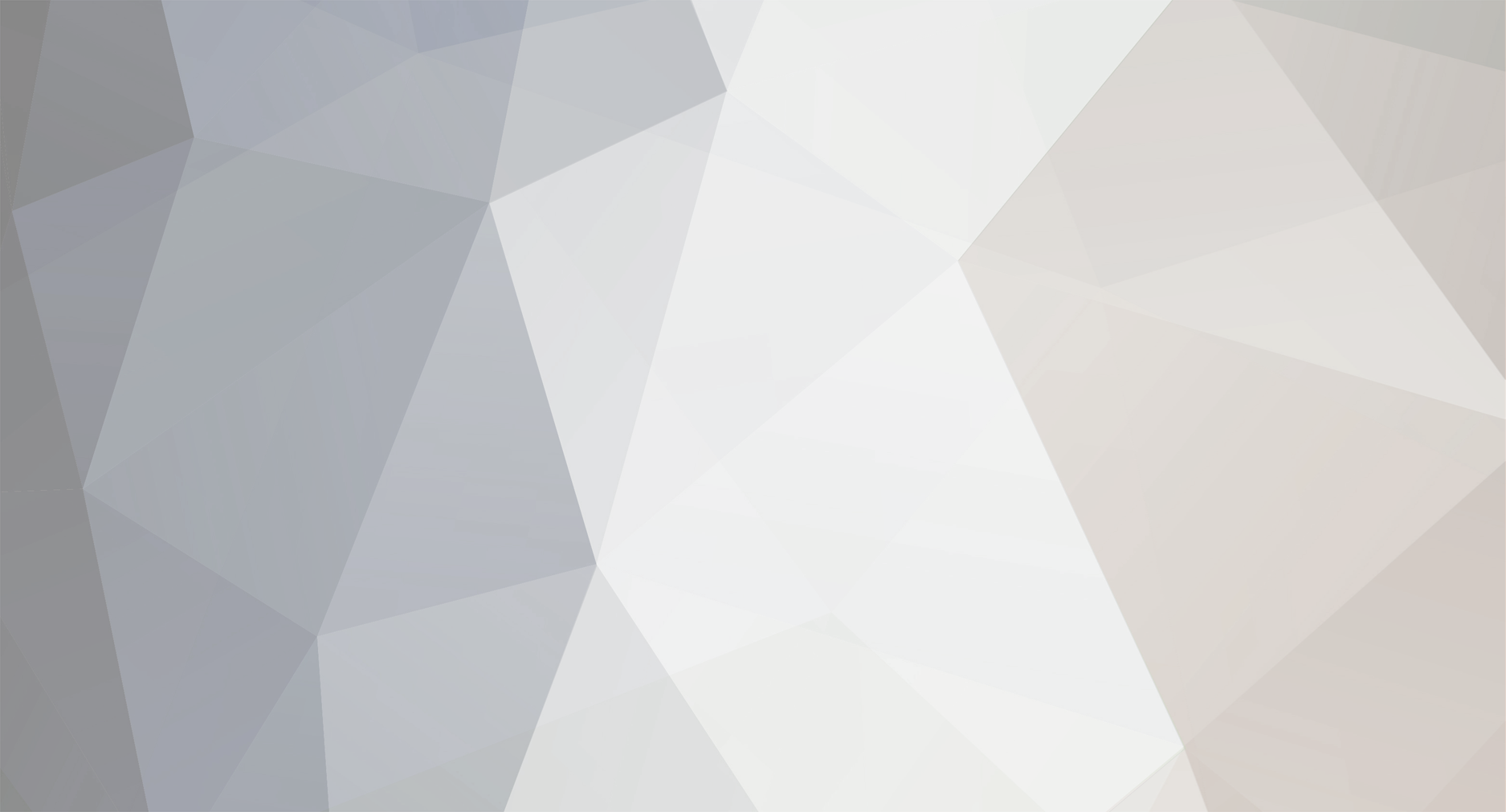
Hobbes
Members-
Content Count
15 -
Joined
-
Last visited
About Hobbes
-
Rank
Snap-Together
Recent Profile Visitors
The recent visitors block is disabled and is not being shown to other users.
-
If you're up for a little scratchbuilding: I've designed some parts (e.g. engine section, Dragon capsule, landing legs) for 3D printing, these are available via Shapeways. I started out in 1/144, in this scale the rocket body is a 1" tube (readily available in e.g. PVC in any DIY store). Then you need some styrene stock for the conduits. Some other scales are available as well. More information on my website: http://www.acme-engineering.nl/
-
Good reference books to help update the Revell 1/144 ISS
Hobbes replied to gmat's topic in Real Space Modeling
The On-Orbit Assembly, Modeling, and Mass Properties Data Book contains drawings of each ISS configuration since the launch of Zarya. Volume 1, 2002 Volume 1, 2008 (despite the name this seems to be a sequel to volume 1, 2002) I haven't found a more recent edition than 2008. -
Scale Model World is well worth it, it's a massive show (2 days is barely enough to see all the exhibits). Not much in the way of space modeling though (LVM, 2 space-related SIGs, and me at the Project Cancelled SIG), but that's true of almost any model show. You could also combine your visit with a trip to the National Space Centre (http://www.spacecentre.co.uk/) in Leicester (100 km from Telford).
-
I haven't ordered anything in FXD yet, so don't know how it compares.
-
That's something I'm struggling with as well. I'm scratchbuilding a rocket at the moment, and I've used my lathe to square off the tube sections. Otherwise, you could place the rocket body in a mitre box and use that as a guide for sanding: that makes it a bit easier to see when you're at an angle.
-
I don't have much experience building rockets, but I'd try this: - use a slow-acting glue so you have plenty of time to do final adjustments. - you need to align 2 points that are 90 degrees apart. If these line up, the rest should be in line as well. - place the upper stage, then place a ruler against the lower stage. When the ruler is flush with the lower stage, it will push the upper stage until it is flush as well (of course this only works if there's nothing on the surface to get in the way). Move the ruler 90 degrees, then repeat. - repeat as necessary until you're happy.
-
The most non-intuitive part of Solidworks is that dimensions and locations are undefined until you add a measurement or specification to your sketch. I've had that issue a few times with profiles I wanted to revolve as Bill describes. Despite drawing one edge of my profile on top of the centerline, Solidworks refused to revolve the profile until I specified the profile edge to be coincident with the centerline. Otherwise, a few tutorials (Youtube is full of 'em) will get you a long way. And practice. You have to do this regularly, or you'll forget how it works.
-
I've been going through this amazing thread, came across your method for scratchbuilding a cone. I've tried this technique a few times to make cylinders, but I could never get one that was properly cylindrical. If I overlap the ends of the styrene sheet, there'll be a jump in diameter. If I use a butt joint the joint will be very weak, so I'd place a piece of strip underneath - but then this would distort the curvature again, creating a flat spot. How did you do yours?
-
I've been using Alabastine, which is readily available in the Netherlands, probably not so much elsewhere.
-
I've been using filler from a spray can on my WSF parts. Simple stuff from the home improvement store will do. I tried using Future to saturate the pores, but after several dips I hadn't made much progress, it seemed, so I stopped that and went straight to primer. I wouldn't use a wire brush. WSF is a sintered powder: if you remove a grain, you just expose another that's just as rough. In my experience, coarse sandpaper would just leave big gouges in the WSF making it harder to get a smooth surface. The quickest way to a smooth finish is to just wet-sand the parts once, and then start sp
-
Not really a kit at the moment. I've made some parts like the engines, Dragon and payload fairing for the Falcon 9 (v1.0 or 1.1). You can combine these parts with commonly available 1" tubing and some scratchbuilt parts like the cable tray and fuel lines (easily made from styrene stock). The parts are available in my Shapeways shop. And I've made instructions as well.
-
Halfway through deciding which CAD program I'd use, I got access to SolidWorks through my employer, so I stopped searching for low-cost CAD tools. If I didn't have that, I'd try FreeCAD. I looked at Blender briefly, but its user interface is so nonstandard it adds considerably to the learning curve. I've also done some work in AC3D (which is about $80), but that's not really suited for 3D printing. AC3D is a surface modeler, which means your object consists of surfaces only. Instead of a cube you get six rectangles which happen to be in the right place to enclose a volume. In complex shapes,
-
Nice job on the nozzles. I've found Shapeways will accept a bit of a 'knife-edge' on the end of the nozzle, this makes the wall look thinner than it really is. You can see it in the image on the left: (that's a 1:144 engine set for the SpaceX Falcon 9, by the way)
-
That blob is a printing defect. I had a similar defect on one of my models, and got a reprint without the defect when I complained.
-
Different Hobbes here :) Frosted Ultra Detail (FUD) parts are printed using a support wax. This material makes the FUD look translucent. When you wash the part in white spirit, the wax dissolves and leaches out, and what's left is a white resin with a slightly grainy surface texture. You can then sand the part smooth and it'll stay that way. I've got a few parts lying around that I cleaned and sanded a few months (up to a year) ago, and they're still smooth. You can also get parts that dry up part translucent and part white. This depends on the orientation of the part, and where the suppo