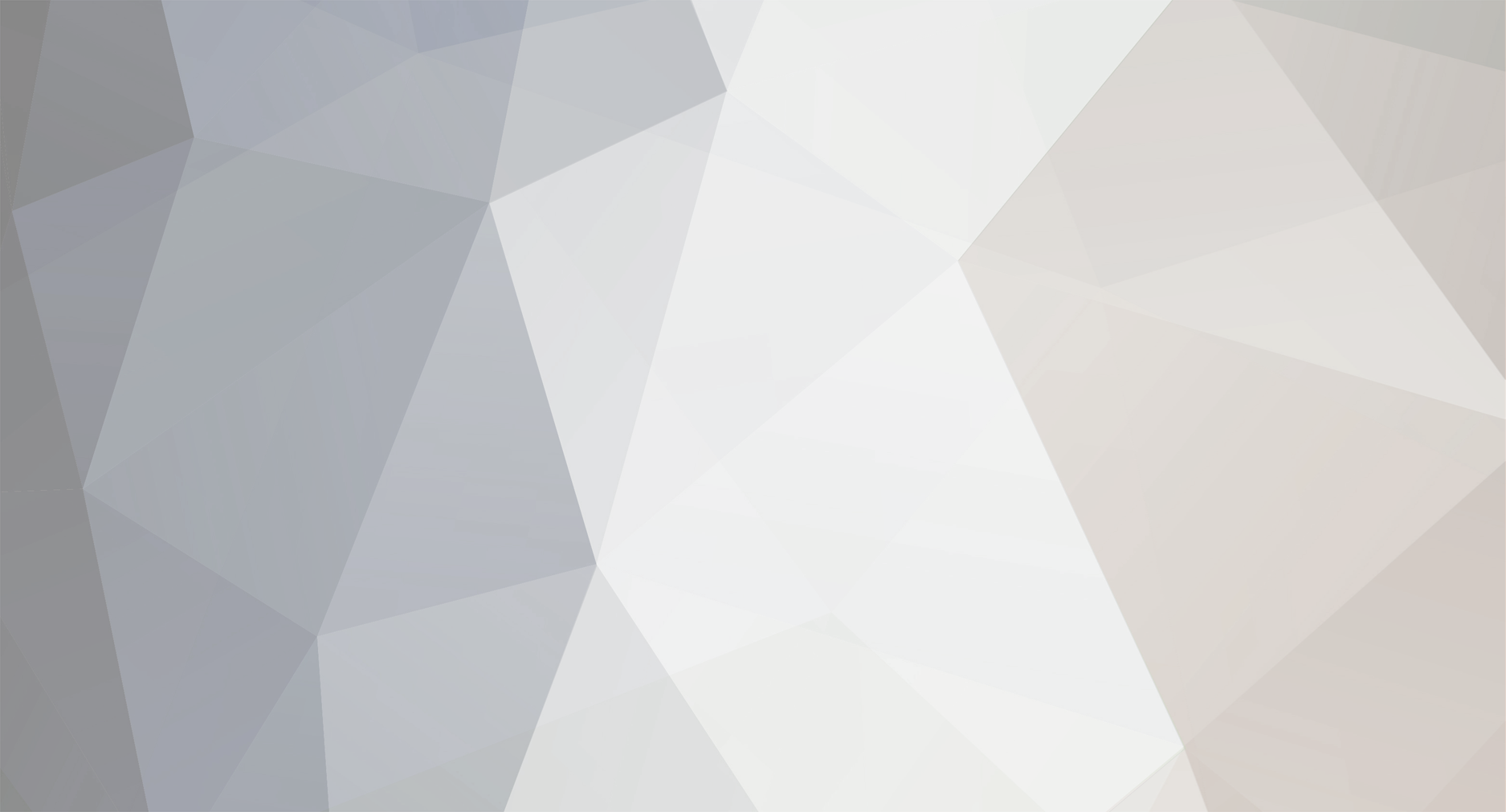
Raymond Chung
-
Content Count
921 -
Joined
-
Last visited
-
Hi Raymond - is there any way I can order just a decal sheet from kit 48096? I would gladly pay the cost of the sheet and the shipping. Thanks in advance.
John
-
Kinetic #48160 F-16A/B ROCAF Missing Decals?
Raymond,
I ordered the Kinetic Gold F-16A/B Block 20 ROCAF kit #48160 through www.squadron.com After receiving the kit, I observed that this kit #48160 has the same markings as kit #48055 since the markings guide and one of the decal sheets has 48055 printed on them.
When I received my #48160 kit I noticed it was missing one of the three decal sheets that appear to be included in #48055. My kit #48160 contained these two sheets:
https://www.1999.co.jp/itbig39/10397673n11.jpg
https://www.1999.co.jp/itbig39/10397673n10.jpg
but this third sheet was not included:
https://www.1999.co.jp/itbig39/10397673n12.jpg
I requested a replacement sheet from Brandon at Squadron, he replied that all of the #48160 kits he received from Kinetic only had the first two decal sheets. Without the third sheet none of the ROCAF decal options in this kit can be built, including the scheme depicted in the box art. Should this third sheet have been included in kit #48160? And if so, how can I obtain the third sheet to complete my kit?
Greg (Habu2)
gdfieser@gmail.com
(I tried sending you a private message via ARC but it says you cannot receive messages?)